"NIMDC" can provide technical specifications for procurement of monitoring instruments and associated softwares and help in installing them.
- Monitoring System (TSI)
- Transducers
- Software
- Portable equipments
Machinery Diagnostic Services
Experienced specialists are available to identify, document and solve your machinery problem and trouble shoot the same by using Advanced Data Acquisition, Monitoring, Analysis and Diagnostic equipment. MDS can meet your requirements for:
- Predictive Analysis of machinery problem
- On-site and Remote Diagnostics, MDS methodology is the same. We use all available data and latest techniques to thoroughly examine the machine for fault. MDS is experienced in diagnosing Unbalance, Shaft Bow, Misalignment/pre-load forces, Fluid In-stability (Oil whirl and Whip), Shaft Cracks. Rubs, Rotor and Structural Resonance, Thrust and Torsional vibration Problems, Surge, Gear problem, Cavitation and Re-circulation, Loose parts, Foundation problems, Assembly errors, Thermal Rub (Partial and annular rub), loading and unloading etc. during Pre and Post overhaul and field commissioning
- Turbine Monitoring, (Steady State and Transient Data) Acquisition and Analysis
- Turbine Trouble shooting and In-situ Multi-plane (Dynamic) Balancing
- Fluid film bearing and Rolling element bearing defect diagnosis
- Electric motor Monitoring and diagnosis (Cracked rotor bar, Current induced bow, Magnetic Unbalance, Non-uniform air gap and High resistance joints).
- Transformer Monitoring ( Dissolved Gas Analysis, Frequency Response Analysis , Partial Discharge Analysis )
- Root Cause Failure Analysis
- Machinery Alignment
- Acceptance Testing
- Consultation
In Today's competitive economy, you are constantly called upon to make rapid decisions about your machinery that impact profitability. You must keep your processes up and running efficiently, while extending the life of the machinery and reducing maintenance cost. When critical machinery shows signs of distress, operating decisions become complex. You must guickly decide not only what to do, but how to do it, in order to maximize overall profitability. This requires rapid access to actionable information for which these methods are used by us.
"NIMDC" can collect vibration data and presents in many formats, based on machine speed (rpm) or time, to assist in trouble-shooting machine malfunctions and analyzing machinery behavior.
-
Shaft Centerline Plots and Eccentricity Ratio- These plots are useful for observing changes in the average position of the rotor in the radial bearings. Changes in shaft centerline position can provide warning of major changes in the adjustment state of the machine.
- Orbit Plots- These plots are used for examining the magnitude, frequency, phase angle and shape of the dynamic motion of the rotor.
- Bode and Polor plots (SAF)- These plots provide mode shape information and can assist in diagnosing shaft cracks. They are also used to document the presence of balance resonances and to determine the SAF of system.
- Full Spectrum- The full spectrum is based on the rotor vibrational data from X-Y transducers. The Fourier transformation splits the original waveforms into frequency components.
- Spectrum Cascade/ Waterfall Plots- These plots show individual frequency spectrums as a function of rpm or time. They are used to track changes in spectral content during a start up or coastdown or over a period of time.
-
- Gap voltage plots- These plots are used to show changes in gap voltage from a proximity transducer to be studied with respect to time or rpm.
- APHT Plots for crack detection.Amplitude & phase changes which are presented as a function of time are called APHT plots.These plots have proved to be very useful in shaft crack detection.
- It is designed to enhance & support your decision making process by reducing the time required to reach a quality diagnosis of a machinery problem.
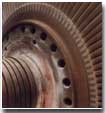